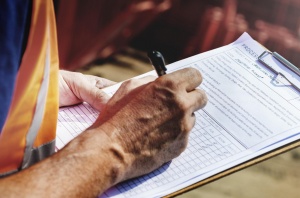
QMS, also referred to as quality maintenance system, is a structured system developed to create an archived report of the procedures, processes, and responsibilities regarding the accomplishment of quality standards and objectives that will ensure that quality product and service is consistently delivered to customers. The activities in an organization are directed and coordinated through a QMS to meet both regulatory and customer standards for effective performance and productivity.
The QMS report needs to make precise and compact documentation of the procedures, processes, and structure of the organization.
U.S Rigging Supply, a manufacturer of rigging & safety equipment, acknowledges that a properly developed framework having proper documentation offers several benefits including guaranteed achievement of quality standards, limits every possibility for errors, minimizes downtime during deviations through effective analyses and access to relevant data that will facilitate simple monitoring of the procedures which will enable a proper analysis of the process output to prompt adequate adjustments. QMS reports achieve several criteria like offering proof of conformity, information distribution, and distributing knowledge which requires different kinds and levels of documents. For instance, quality policy, quality manual, work guidelines, and recorded procedures.
A multipurpose feature is usually not ideal as every type of document must match its purpose which will enable it to be understood easily by the required personnel and facilitate proper implementation. Documentation needs to be brief because excessive documentation can yield a more difficult usage and maintenance for the procedures and individual QMS and at the same time being bureaucratic. Also, documentation is needed for regulatory standards that need to be established for effective operation, control and planning of the organization’s procedures together with the execution and continuous advancement of its QMS performance. Proper documentation proves to be vital to an effective QMS and as a matter of fact, it forms the basis of the QMS of an organization as it offers efficiency to the QMS for the product/service life cycle that will be delivered. The steps provided below are vital in optimizing documentation.
Step 1: Recognition of Documentation
Use a Process Map to recognize every process and communication involved. This process analysis will assist in determining the required documentation for the QMS. Standards of QMS will help to identify the compulsory documents. For instance, ISO13485:2016 outlines the quality policy, quality manual, quality records, quality objectives and six processes that are provided in the list below as compulsory documentation.
- Control of Records
- Control of Documents
- Control of Nonconforming Product
- Corrective Action
- Internal Audit
- Preventive Action
Subsequently, the appropriate procedure will be required to act as coverage for every section of the standard that is applicable to your business and the level and number of documentations that would be implemented would be determined by the business complexities.
Step 2: Recognize the Documentation Structure
The structure of the documentation can be applied to every organization irrespective of the complexity and size of the organization and we suggest that every organization implements this structure.
Documents Hierarchy. Figure 1 analyzes the ranking of regular QMS documentation having various types of document at every level is outlined below.
Quality Manual
This explains the QMS that has been established as well as the activities of an organization to execute the QMS. Contained in the Quality Manual are the focused area of the QMS, the references for recorded processes, the information about and rationale behind every exclusion and detailed information on the QMS procedures as well as the communication involved which is usually displayed in charts.
Quality Procedures
This explains the process used by the organization to execute the QMS by recording the appropriate procedures. These formats comprise flowcharts, texts, tables, together with a combination of these formats depending on the requirement of the organization. The processes are regularly compared with the work instructions.
Work Instruction
This explains the operations covered in a process as well as a comprehensive description of how the tasks are carried out and documented. The format, structure, and degree of specifics that are needed are determined by the training that as initiated, the complexity of the job and the expertise of the workforce that implements the work instruction.
Quality Records
This is used to provide proof that every required operation and process within an activity has been documented by an organization.
Step 3: Develop QMS documents
The processes, structure, and procedure of an organization are recorded in QMS documents as well as the generated outcomes from a quality product or service that is delivered to customers on a regular basis. Proper documentation facilitates proper awareness of the procedures by the workforce for appropriate implementation and documentation as quality records. This implies that documents should be readable, with the use of easy and well understandable language, brief and have a logical flow naturally. These characteristics will facilitate a proper understanding of the conveyed information and content. Expending time and efforts during this stage to ensure the required standard for the document will save subsequent time and effort during the review of the documents.
The process owners should be responsible for developing the documents as they have adequate knowledge about the processes involved. The initial document that should be developed is the quality procedure which is used by the document to manage the procedure that would be primarily drafted. The control procedure of the document is responsible for providing information about the arrangement of all the types of documents covered in the QMS which makes it the initial step when developing the documentation of a QMS. The control procedure of the documents is used to resolve the following
Analysis and authorization of the document for relevancy before an issue.
Analysis of the document as well as important updates and re-authorization.
Facilitates proper review status of and document modifications that are identifiable.
Facilitates the accessibility of the appropriate versions of relevant documents when required.
Guarantees the legibility and proper recognition of documents.
Facilitates the recognition of external documents as well as proper distribution.
Avoids unplanned utilization of outdated documents and the application of appropriate identification to these documents.
Subsequent quality procedure documents that should be developed are the ones that are determined according to the standard set by the organization and the Quality manual that will be credited to the document can be developed during the document drafting process.
The final document to be developed will provide complete coverage of every section of the standard that is relevant to your business. The work instructions can then be drafted after every of the quality procedures have been developed. Then, the developed work instructions should then be reviewed against the Quality Manual to ensure that a precise overview of the QMS is provided.
Conclusion
Proper documentation enhances the productivity and efficiency of an organization by establishing a solid foundation for your QMS. Achieving proper documentation for your organization only requires you to follow the 5 fundamental procedures indicated above especially if the process is just being developed. In a situation where the documentation of your QMS requires an update, you have to determine the section that is responsible for the issue such as the structure, content or both which can be performed by verifying your QMS documentation.
At RRL, we can assist in the design, development, and implementation of quality documentation as well as an effective and productive system of documentation for your organization or provide the required assistance in the update of an existing documentation to make sure it perfectly fits your standards and simultaneously guarantee that it delivers optimum product/service to your clients.